Josh Sellers uses technology from electronic monitors to provide yield information (above)
by Linda L. Esterson, photography by Nikola Tzenov
Innovation Reshapes Farming
CARROLL County was founded as an agriculture and farming community, and when we think of the tradition of farming here, visions of older men in overalls with pitchforks and straw hats come to mind. We think of overworked farmers sitting atop open tractors with tremendous wheels that plowed through the fields from before dawn to after dusk. Generation after generation worked on the family farm, planting, weeding and picking crops.
Today’s farmers look very different, and their methods have evolved. The new vision includes automation, air-conditioned tractors with computers on board, cows wearing Fitbit-like devices and apps that allow farmers to see every single seed being planted on their farm. They have welcomed the use of technology into their practice, and, like the consumer, are reaping the rewards. Despite many farms being turned into neighborhoods and the population booms that come with it, farming and agriculture are more important than ever.
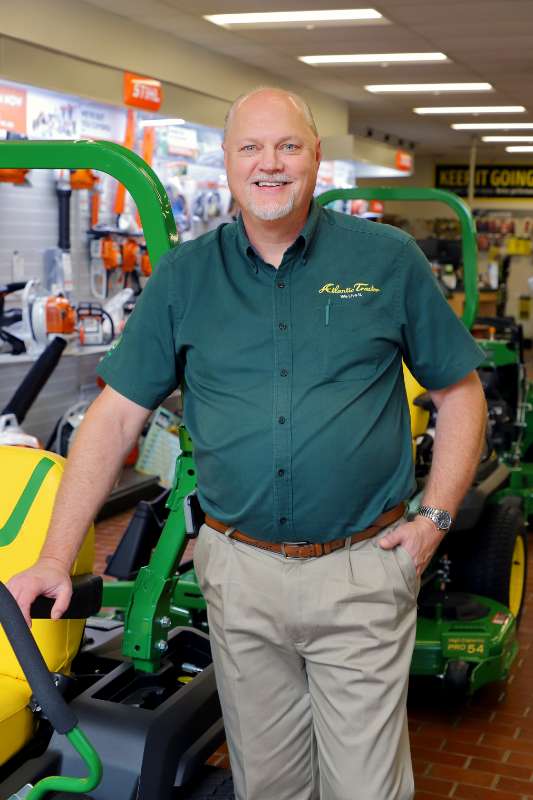
“They’re riding in comfort nowadays. It’s big difference from your grandfather’s [tractor]. They’ve come a long way.” –AARON BOGGS, ATLANTIC TRACTOR
The first technology utilized on farming equipment, Boggs notes, was the auto steering mechanism. Using a GPS tracker, farmers could establish parameters to enable the equipment to self-drive. Today’s equipment also includes the ability to pull data in real-time and track distance, time and the amount of product used. For instance, cameras the size of quarters detect plant growth to determine what needs to be sprayed, whether pesticide, insecticide, herbicide or fertilizer, amounting to about 60 percent savings in fuel and chemical use.
“That’s less chemicals going into the waterways and eventually the Chesapeake Bay and in our area,” Boggs says. “And the savings to the farmer is tremendous. It’s evolved from collecting data as it goes along to making it easier to access and more usable. Customers can make decisions in real time … and adjustments.”
Bud Stambaugh, one of six family members who operate Pheasant Echos Farm in Westminster, says he has seen enormous growth in the use of technology in both their dairy and row crop operations, since his parents Barney and Debbie Stambaugh purchased the farm in 1991. The greatest growth, he says, is in the equipment, specifically the tractors, planters and sprayers used on their 2,500-acre row crop operation. They grow corn, soybeans, wheat, barley and string beans. By investing in new technology, the business has seen a 25 percent growth in productivity.
“Anytime you invest in the equipment, you invest in extra technology, and it’s trying to make you more productive and leave less of a footprint on the environment,” he says. “The GPS tracks where the equipment has been, where it applied the feed or pesticides or fertilizer. And it turns itself off when it knows it has already been there.”
The technology reduces labor and speeds up the processes. It also uses less product “because we’re putting it exactly where it belongs.”
Today’s equipment is also built for comfort. The cabins have air-conditioning and heating with Bluetooth stereos and digital screens. The technology reduces stress, as the farmer can accept phone calls without stopping and continue for longer periods with reduced fatigue.
“They’re riding in comfort nowadays,” Boggs says. “It’s a big difference from your grandfather’s [tractor]. They’ve come a long way.”
Software programs control specific tasks — and with the push of a button, planting can begin with precision. The depth of the seed, the distance between seeds and the space between rows are all predetermined and administered using the advanced equipment. A newer device, called the exact shot, also sprays the seed with starter fertilizer during the planting process.
“It has everything to do with quality and how fast it can grow,” Boggs adds. “It just sets up the perfect conditions for that plant, based on years of agronomy work and university research.”
But the technology comes with a cost. A machine called a combine with corn head, which performs the harvesting of corn, retails new for $1 million. A new 8R tractor retails for $600,000, and planters go for about $250,000.
This season, the Stambaughs purchased a two-year-old combine for harvesting, which runs more efficiently and collects detailed data, enabling greater analysis than ever before. They will be able to evaluate inputs — seeds, fertilizer and application methods and timing — to compare with harvesting yields this fall. They also added a new sprayer at a price of around $700,000. To justify the cost, they operate another company, Uniontown Ag Services LLC, which provides spraying services to nearly 50 producers in Montgomery, Frederick and Howard counties, and as far north as Hanover, Pa. They also provide custom combine services to other farms.
The Sellers family, operator of Panora Acres in Melrose, has also embraced technology to advance production, but they did it gradually. About 10 years ago, they adopted auto-steering for planting, and it grew from there, according to Josh Sellers, the sixth-generation family member to work on the farm.
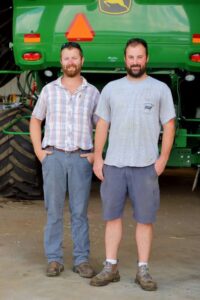
Bud and Kenny Stambaugh operate Pheasant Echos Farm in Westminster along with four other family members.
Today, with the help of technology, Josh does the majority of the field work on the farm’s 1,800 acres, which consists of planting, spraying and harvesting primarily corn, soybeans and wheat. The equipment covers more area and makes the processes more efficient, he says.
“Thirty years ago, you had to have three or four planters and plenty of help,” he says. “It was different.”
Sellers switched to a variable-rate spreader this year, and used strip tilling for part of the planting. This enabled tilling and fertilizing at the time of planting, with software that provides prescription maps and instills limits that produce an accurate application to about an eighth of an inch. He expects to convert to 100 percent strip tilling next year. The technology provides yield information which improves decision making, he adds.
Ten years ago, a flat rate of fertilizer mix was spread across the full area. Some areas received too much and others not enough.
“In the olden days, you would just plant, and if it didn’t work, then the next year you planted somewhere else,” he says. The ability to monitor and vary the rate of application to where it is needed has lowered costs and increased productivity, he notes. Using an app on his phone, he can remotely view the screen on the tractor and assist staff in the field if he’s away from the farm.
“You want to be more precise and track what you’re doing a lot better,” Josh says. “No matter where I am or what I’m doing, I can get on my phone and pull up an app and I can see everything that has been done to that field.”
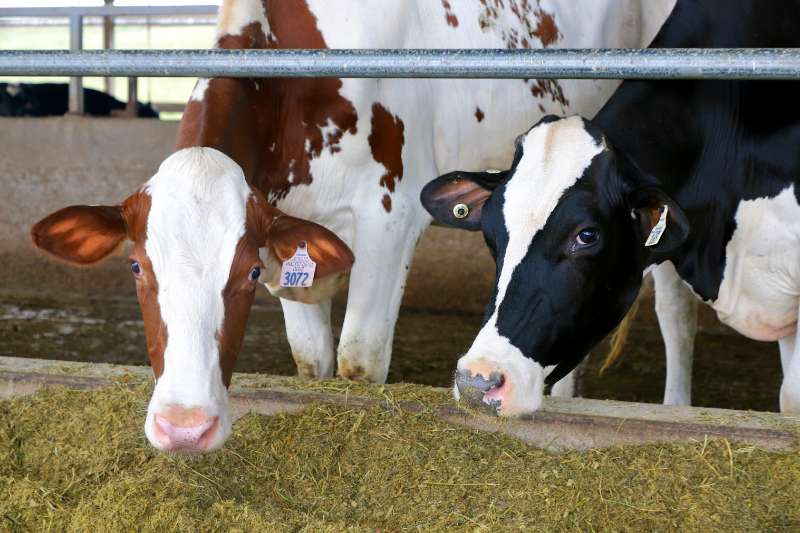
“The cows are fed in a trough, and a robot device, also added about six years ago, pushes the food to the front of the trough every few hours to keep it easily accessible. This saves labor, and increases production as the cows always have mixed feed in front of them.” –BUD STAMBAUGH, PHEASANT ECHOS FARM
The Stambaughs have also added technology to improve their dairy operation. When they started milking cows, milkers were hooked to a vacuum line and a pulsator line that squeezed out the milk. The device was closely watched to prevent damage to the cow’s flesh if left on too long. It was carried from cow to cow.
After about six years, they bought an automatic takeoff, which included a sensor that indicated when the milk flow slowed. The sensor triggered a string that turned off the vacuum and removed the milker from the cow.
This didn’t impact production per se, but the next additions did. The mix wagon enabled the creation of a custom mix of feed and grain that is weighed before providing it to their 150 Holstein cows.
“That way, they were getting the right amount of food and there’s not as much variability in it from day to day because you’re mixing it so well,” Bud explains. “I would say that’s where they first saw a jump in production.”
Production was also aided by the transition to a free stall barn, in which the cows rest on beds of compost. While the cows are milked in the parlor, the bedding is tilled by a rototiller that composts the sawdust and wood shavings and at the same time uses heat to kill the bacteria that results from their excrement to create a healthier, cleaner and softer space. Better rested cows also yield more milk.
For the last 10 years, the farm’s cows have worn pedometers, similar to a Fitbit, that tracks their steps and their activity. Software sends alerts if a cow is restless, if they are in heat, or low in activity, possibly signifying an illness. Along with the pedometers, meters in the milking parlor track production and test conductivity of the milk. Deviations can indicate a problem.
The robot feeders cost $30,000 and the pedometers $60,000. “Nothing in today’s world is cheap,” Bud says. “[When] you look at something that costs that much, you work numbers the best you can and see if it’s going to justify itself. Everything we’ve done so far has [given us] a return on that investment.”
Bud estimates the use of technology in the dairy operation has generated an increase in production of 15 percent to 20 percent.
“It’s decreased some of our labor and made us more productive,” he says. “And it’s helped us to all in all make higher-quality milk products.”
—————————————–